I. Introduction
Energy supply & demand and global warming caused by climate change have emerged as urgent global problems in recent years. In this context, the Korean government set the target of reducing 30% of 2020 BAU; and in its 2009 plan for the vitalization of green city and buildings, decided to reduce 26.9% in the section of buildings(home and commercial) that accounts for 25% of the national greenhouse gas emissions(Ministry of Land, Infrastructure and Transport, 2009). Based on this scenario of greenhouse gas reduction, the government announced a road map for reducing 50% of cooling and heating energy in 2012, and requiring all new houses to comply with the standards of passive house from 2017 and those of zero energy housing from 2025.
In addition, according to the press release of June 2015, the government decided and announced its own 2030 target to ‘reduce the country’s greenhouse gas emissions by 37% from the business-as-usual(BAU) level (851 million tons)’ prior to the post-2020 climate regime to be formed in December. It is expected that the post-2020 climate regime agreement will be adopted in COP21 to be held December in Paris on the basis of each country’s submitted INDC (intended nationally determined contribution).
Therefore, it is now important to pay attention to the post-2020 climate regime that will apply from 2020. Submitting the target for reduction, the government announced that it would actively foster and expand new energy industries as creative and epoch- making for reducing greenhouse gas, and improve support system, rather than imposing regulations, so that industries may make spontaneous efforts to save energy and reduce green gases through the market and technologies. On this, since 2009, the Ministry of Land, Infrastructure and Transport has worked out the green policy and has carried out model projects for the dissemination of green home and the vitalization of zero energy buildings.
The reality, however, is that the air-tight high-performance window and the outside heat-insulation wall method, which are core passive element technologies for the implementation of zero energy buildings, have not been widely distributed in the market. There are various reasons for this, but rising costs are the biggest reason. Therefore, for the dissemination of passive houses, the cost efficiency of core passive element technologies should be secured first, which will make it possible to create the residential space pursuing sustainability, amenity, and economic feasibility for future apartments as well as to achieve the policy target of the government.
The purpose of this study is to provide basic data needed to analyze the economic feasibility of the passive multidwelling unit (hereinafter MDU), for the 2017 Dissemination of Passive Multi-Dwelling Units, a major plan for the reduction of national carbon emissions.
The economic evaluation of passive MDU can be performed in terms of the payback period calculated with the saved heating energy cost and increased construction cost of passive MDU compared with the costs of general MDUs. However, there is difficulty in the economic evaluation, for there is no clear definition on the standard model of general MDUs, which serve as the criteria for the economic evaluation. For reliable economic evaluation, an analysis for setting the criteria should precede, and methods for enhancing economic feasibility should be worked out on the basis of the analysis.
For the economic evaluation of passive MDU, this study developed general MDU models and a passive MDU model, and calculated the heating energy demand and the construction cost for each model through simulation. For the evaluation of energy performance in the general MDUs, which serve as the criteria, the Standard for the Energy- saving Design of Building (Ministry of Land, Infrastructure and Transport, 2001-2013) was applied. The Standard for the Energy-saving Design of Building raised criteria for heat insulation performance through its several revisions after 2001. To reflect this, four models, to which criteria for heat insulation performance pursuant to 2001, 2008, 2011, and 2013 Standard for the Energy-saving Design of Building were applied, respectively, were selected as general MDU models by year for economic evaluation. Further, windows and insulation parts that met relevant thermal insulation criteria were selected, and the construction cost of a system selected from the Monthly Price Information(Korea Price Research Center, November 2014) was calculated.
For the passive MDU model, an 8-storied zero carbon green home MDU, a passive house constructed 2012 in Goyang-si, was selected. The construction cost was calculated with the unit prices of passive element technologies used in the zero carbon green home, that is, the unit prices actually applied at the time of construction(Zero Carbon Green Home As-built Document, 2012). Factors that influence the economic evaluation of passive MDU are the saved heating energy cost and increased construction cost of passive MDU compared with the costs of general MDU. The biggest factor in the variation of heating cost is the differences in the thermal insulation performance of general MDU by year, which vary heating cost greatly, and ultimately influence the economic feasibility of passive MDU. In the case of construction cost, actual construction cost reflects the bid price rate, and thus the economic feasibility varies according to the bid price rate. Therefore, reliable economic evaluation requires an economic analysis made in consideration of the above factors of variation.
The method and procedure of this study are as shown in Fig. 1.
First, institutional changes in the standard for the energy-saving design of domestic buildings, and the results of residential building construction were investigated in order to analyze the energy performance characteristics of general MDU; and trends of domestic studies on passive houses were reviewed.
Second, the heating energy demand and the construction cost were calculated with the general MDU models, which follow the Standard for the Energy-saving Design of Building according to the years, and the passive MDU model, to which the zero carbon green home validation housing was applied; and differences in them between the models were analyzed.
Third, factors in the reduction of heating cost and construction cost, which influence the economic feasibility of passive MDU, were derived.
Lastly, the construction completion years of general MDU models acting as the criteria were suggested by analyzing economic feasibility according to the general MDU models by year and bid price rates.
II. Theoretical Review of the Study
In 2013, the government published and enforced the Green Building Construction Support Act in order to disseminate and expand energy-saving green buildings, with the target of all new buildings being passive houses by 2017. In addition, the government revised the ‘Standard for the Energy-saving Design of Building,’ a detailed architecture standard, and it was stipulated that standard scores or higher should be obtained in the evaluation of the application levels of elements such as thermal insulation and equipment.
After the Building Act was enacted in 1976 to prevent heat loss from buildings, the government repeated its revision from time to time. As it became necessary to strengthen the energy efficiency of buildings in order to cope with the Framework Convention on Climate Change and the era of high oil prices, the government began to promote efficient energy saving by improving and strengthening in 2001 the ‘Standard for the Energy-saving Design of Building’ (Ministry of Land, Transport and Maritime Affairs Notification No. 2001-314) focusing on the prevention of heat loss from buildings, as shown in Table 1. Since the revision in 2001, the standard of heat insulation has been strengthened 20% on average, and the heat performance of window, which has the greatest effects on the heat loss of a building, was subdivided into the overall U-value including window frame and pane.
After the 2009 policy on the vitalization of green city and buildings, the standards for the thermal insulation performance of skin as well as window were greatly reinforced from 2011.
The results of domestic housing construction by year and the distribution of housing by type were investigated to find out the distribution of MDUs among the whole housing. The results of domestic housing construction were analyzed, using the Statistics of Housing Construction (Statistics Korea, 2015) from the KOSIS (Korean Statistical Information Service), a portal of the Statistics Korea. As shown in Fig. 2, the results of housing construction from 1995 to 2014 show that in the 1990s, the annual average construction performance of 600 thousand houses was maintained before the foreign currency crisis in 1998, but decreased to 300 thousand houses in 1998. In 2001, the housing construction sharply increased again to 670 thousand houses, then decreased again after the global financial crisis in 2008, and maintains the annual average construction of 500 thousand houses in 2014.
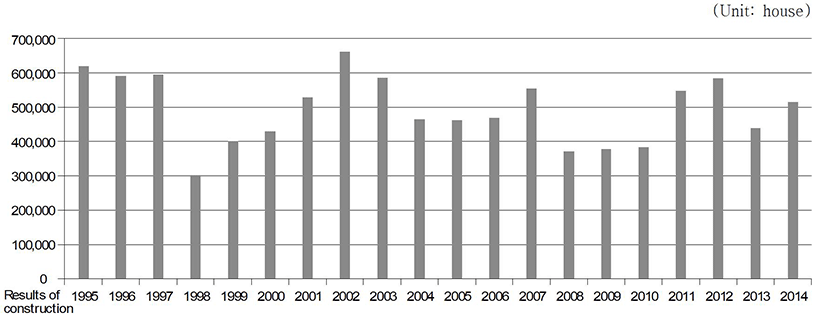
In addition, as shown in Fig. 3, the analysis of construction results by housing type shows that MDUs including apartments and multi-household houses accounted for 59.3% of the whole housing and exceeded a majority after 2000, and that a large majority 71.6 % of the domestic housing were MDUs in 2010. Consequently, this study carried out research, selecting MDU as the representative building type of domestic housing.
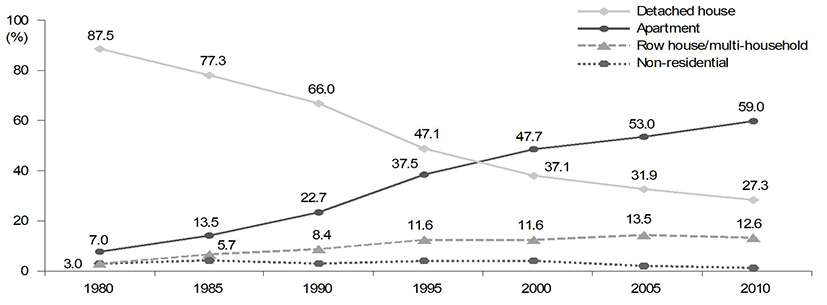
Most studies on enhancing the energy efficiency of domestic MDUs for the reduction of carbon emissions have been concentrated on the energy consumption of MDUs. In a survey on energy consumption at the stage of the actual operation of general MDUs, Park Seol-hui et al. (2014) conducted a survey of 17 MDU complexes, whose construction was completed between 2002 and 2011, with respect to energy consumption in the sections of heating, hot-water supply, electricity, and gas (cooking). Cheong Chang-heon et al. (2010) comparatively analyzed standards for energy performance evaluation in Passive House and those in the building energy efficiency rating system, conducted surveys of energy consumption in actual passive buildings and in building energy efficiency rating certified buildings, and suggested improvements in the building energy efficiency rating certification system.
Most of studies on low-energy MDUs or passive MDUs also address the effects of energy consumption reduction in case of applying specific element technology. Song Seung-yeong et al. (2009) analyzed annual heating energy reduction effects in case of applying external insulation system. Choe Yun-jeong et al. (2013) derived integrated energy performances formulas for window by considering relevant methods for evaluating windows that have the greatest effects on cooling and heating load in MDU.
Like the above, most related studies are concentrated on the energy consumption of buildings. However, the economic evaluation, which should precede for the dissemination of passive MDU, requires investigation not only into the energy consumption of buildings, but also into factors that have effects on the establishment of the standard model (baseline) of general MDU, which acts as the criterion for economic evaluation, and on the calculation of the construction cost of actual MDU.
In addition, the overall energy consumption used by MDU and the share of heating energy in it were reviewed. The Energy Consumption Survey (2008) reported that the annual overall energy consumption used by MDU of 33 pyeong was 15,217 kWh as of 2008, among which equipment accounted for 3,104 kWh(20.4%), lighting 574 kWh(3.8%), heating 7,430 kWh (48.8%), hot-water supply 3,183 kWh(20.9%), and cooking 926 kWh(6.1%), respectively. As for the heating energy, as shown in Table 2, as a result of examining the annual energy consumption by use in MDU on the basis of legal standards in 2008 and 2010, it was found that it accounted for approximately 50%. Thus, this study selected and investigated the heating energy, for the evaluation of the energy consumption according to the MDU models.
The zero carbon green home used as the model of passive MDUs in this study was constructed as an 8-storied passive MDU for 15 households, as shown in Fig. 4. For the optimum design and application of zero carbon green home element technologies, the integrated project delivery (IPD) was adopted (AIA, IPD: A GUIDE, 2007). The zero carbon green home aims at zero CO2 emission at the stage of using MDU, not during the life cycle of the building; and was defined as a building in which the sum of CO2 emissions at the stage of using a building and CO2 emissions reduced by producing energy through new and renewable energy system becomes zero. The energy performance goals of the zero carbon green home are the energy saving of 87% in heating and 80% in electricity, compared with the existing MDUs, and zero CO2 emission at the stage of building operation, through applying the passive system and the new and renewable energy supply system. The types and performance of major element technologies applied to the zero carbon green home validation housing are as shown in Table 3.
III. Comparative Analysis of Heating Energy Demand between General MDU and Passive MDU
Differences in heating energy consumption between general MDU and passive MDU are largely due to differences in insulation methods, insulation performance, and ventilation methods. While the general MDU suffers significant heat loss via thermal bridge at the joint between balcony or floor and wall because the internal insulation method is applied to it, the passive MDU prevents the generation of thermal bridge fundamentally by applying the outside insulation method. They also show a great difference in the insulation performance of window and wall; the passive MDU is 2-4 times higher in insulation performance than the general MDU. Moreover, as for the ventilation systems of general MDUs, most of them are the ordinary air-conditioning system that is incapable of heat exchange, and heating energy comes to increase as much as the amount of incoming ventilation air. As for the passive MDU, however, heating energy loss caused by ventilation is reduced by 80% and above thanks to the application of the heat recovery ventilation system. To compare heating energy demand given these differences in heat insulation and ventilation methods, the heating energy demand of the general MDU models by year and the passive MDU model was calculated through simulation.
The general MDU models by year are classified into four models according to insulation performance in the Standard for Energy-saving Design of Building for relevant years; and heating energy-related element technologies, such as window, door, insulation, ventilation system, and boiler, which met their respective insulation standards, were applied. As for the passive MDU model, element technologies actually used in the construction of the zero carbon green home were applied. Heating energy demand for each model was calculated by using the ECO-Home program (Korea Institute of Civil Engineering and Building Technology, 2012). The ECO-Home program is the upgraded one of a program used from 2001 for evaluating the energy efficiency rating certification of MDUs, and permits the analysis of passive houses. It is a program for calculating the housing energy consumption in which the influence of thermal bridge by external insulation and internal insulation on the existing housing as well as new housing is reflected and the influence of ventilation system and infiltration is reflected.
As for the plan of the MDU to be evaluated, the 6th floor plan, which is equivalent to the middle story of the zero carbon green home, was applied, as shown in Fig. 5; and as for the results calculated from simulation, the mean of two households was applied. The object building is located in the Central Region, and has a full south aspect. As for the MDU model applied, its heating area by household is 105㎡, the floor area of its non-heating space is 14.2㎡, and its floor height is 3m, respectively. In the passive MDU model, the outside insulation method was applied to the common-use corridor, which is a non-heating space, as well as heating space. The general MDU models were set in such a way that the internal insulation method was applied to the same plan, and that a wall in contact with outdoor air at the common-use corridor, which is a non-heating space, was not insulated. In both cases, staircases were set to be outside spaces where outdoor air circulates.
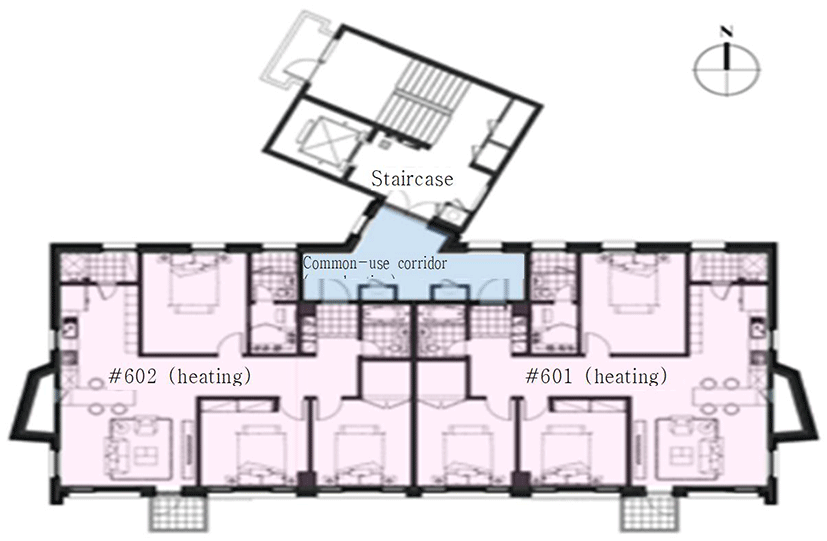
The area of walls and windows, indoor and outdoor setting temperature, and machinery heating value, which are setting conditions common to all the models in simulation, are as shown in Table 4; and insulation performance, ventilation performance, and system efficiency, which vary according to models, are as shown in Table 5.
First, among the results of simulation, the result of calculating the heat loss, which increases heating energy demand, according to the models was analyzed. As shown in Table 6 and Table 7, the total heat loss of the passive MDU was greatly reduced to 25-33%, compared with the general MDUs by year.
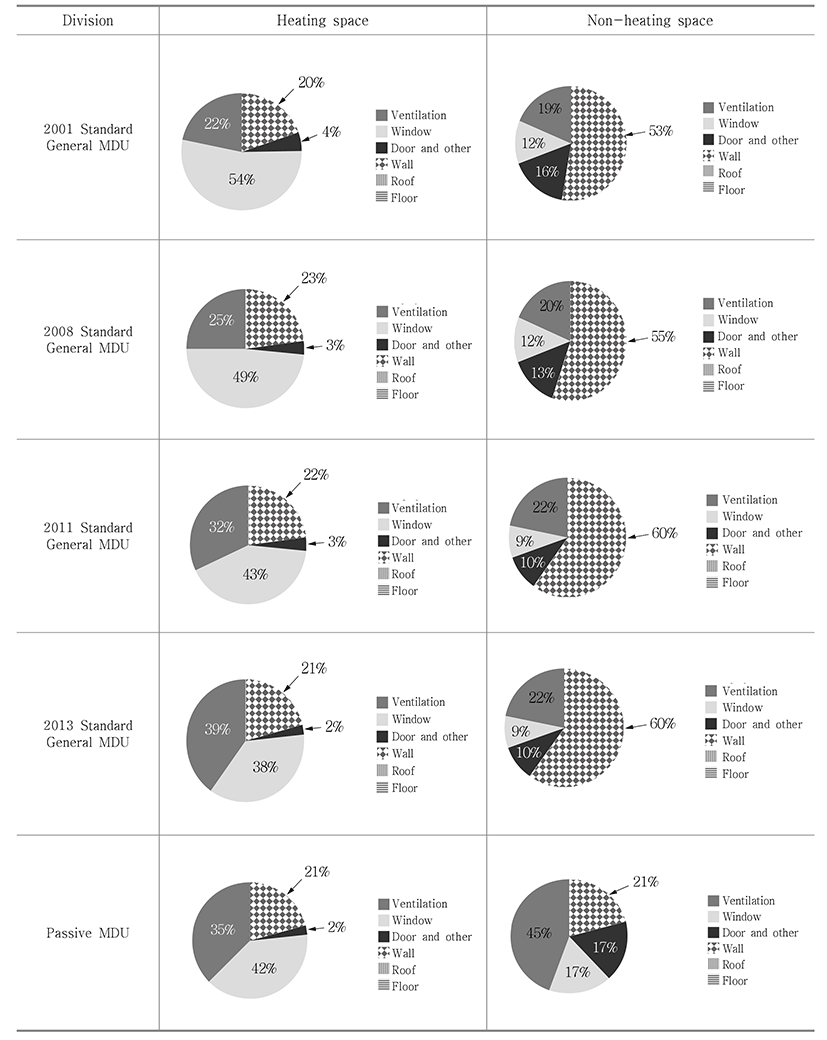
In the general MDU, heat loss from window was 38-54%, accounting for the greatest portion of heating energy demand. And it was found that the heat loss of the ventilation part relatively increased according as the general MDU progressed towards the passive MDU, with its reinforced insulation performance. While at the general MDU in 2001 and 2008, heat loss from the skin through window and wall accounted for more than 70% of the total heat loss, and heat loss from ventilation accounted for 25% and below, the general MDU in 2011 and 2013 showed that the ratio of heat loss from skin accounted for about 60%, which is similar to that in the passive MDU, and that the ratio of ventilation heat loss exceeded 30%. Analysis shows that this was because the standard for the insulation of skin was greatly reinforced from the 2011 Standard for Energy-saving Design for Building. The insulation standard for window in contact with outdoor air was 3.84 W/m2K in 2001 and 3.0 W/m2K in 2008, but was abruptly raised to 2.1 W/m2K in 2011 and 1.5 W/m2K in 2013. That for wall was also raised to the similar level. And thus, the general MDU was analyzed as showing heat loss distribution similar to the passive MDU.
Therefore, the efficiency of the heat recovery ventilation system needs to be improved in the future to further reduce heat loss from the ventilation part in the general MDU and the passive MDU. And energy saving and occupant’s comfort need to be enhanced by applying a silencer to the ventilation duct and a pre-heater to the outdoor air intake part of the total heat exchanger without fail in order to solve the problem that users avoid using the ventilation system due to its noise and low supply air temperature.
Next, the result of calculating the solar heat gain that reduces heating energy demand is as shown in Table 8. The solar heat gain gradually decreases according to progress from the general MDU by year to the passive MDU. This is because the solar heat gain coefficient (SHGC) decreased due to coating and the increase in the number of window panes according to the enhancement of the insulation standard. Particularly, in the case of the passive MDU, the evaluation showed that the solar gain decreased sharply due to the application of quintuple glazing. The solar heat gain of the passive MDU shows low values, 45-69% of the general MDU by year.
The results of calculating the heating energy demand of the passive MDU model and the general MDU model by year in the simulation are as shown in Table 9 and Fig. 6. As a result of comparatively analyzing the annual heating energy demand of the general MDU by year and the passive MDU, it was found that the annual heating energy demand of the passive MDU was 17-36% of that of the general MDU by year, sharply decreasing compared with the general MDU.
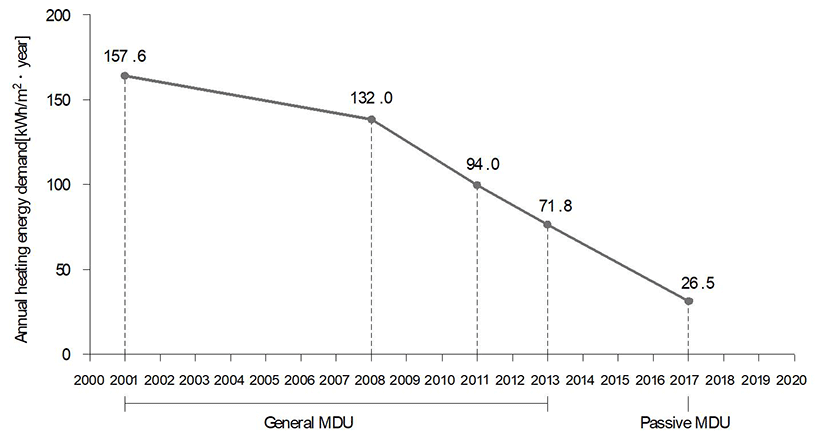
As a result of examining the heating energy demand of the general MDU, which acts as the criterion for economic evaluation, it was found that it changed greatly, with the 2011 model being as the starting point. As shown in Fig. 6, there was no great difference between the 2001 general MDU model and the 2008 general MDU model; with the progress towards 2011 and 2013, however, the models showed the heating energy demand similar to that of the passive MDU, compared with the other models, due to the abruptly raised insulation standard, and thus were evaluated as being improper to represent the general MDU. Therefore, it was judged that it is suitable to apply the 2001 model and the 2008 model as the standard models of the general MDU in economic evaluation.
IV. Analysis on the Economic Feasibility of Passive MDU
For the analysis of the economic feasibility of passive MDU, the saved amount of heating cost in the passive MDU was calculated by calculating the heating costs of the general MDU by year and of the passive MDU, based on the heating energy demand calculated in the above simulation. In addition, the increased amount of construction cost for the passive MDU was calculated in comparison with the general MDU by calculating the construction cost of applied element technologies by model. Here, in the calculation of construction cost by model, the construction costs of framework, electricity and equipment system, which are applied in common to all the models, were excluded. As for the construction costs of the general MDU by year, the construction costs of windows and the insulation system that satisfied relevant insulation standards were calculated on the basis of price data (Korea Price Research Center, 2014). As for the construction cost of the passive MDU, it was calculated on the basis of the unit prices of element technologies that were actually applied to the construction of the zero carbon green home validation house in 2012(Zero Carbon Green Home As-built Document, 2012).
Finally, the standard of the general MDU model, which acts as the criterion, was suggested through the analysis of economic feasibility based on the general MDU model by year and the bid price rate; and the optimum construction cost levels of core element technologies for the dissemination of the passive MDU were suggested.
The annual heating energy demand per unit area and the heating cost per household calculated in the simulation for the general MDU by year and the passive MDU are as follows: In the case of the general MDU, in which a gas boiler was installed, the heating cost per household was calculated on the basis of city gas unit price in November 2014, as shown in Table 10. In the case of the MDU based on the 2001 Standard for Energy-saving Design, the annual heating cost was KRW 1,515 thousand, and the annual heating cost for the MDU of the 2008 Standard was calculated at KRW 1,269 thousand, that for the MDU of the 2011 Standard at KRW 903 thousand, and that for the MDU of the 2013 Standard at KRW 691 thousand, respectively. As shown in Table 11, the passive MDU uses wood pallets, which fall under the new and renewable energy, and thus its annual heating cost per unit household calculated by applying the unit price per heating value of pellet is KRW 234 thousand. As shown in Table 12, the annual heating cost of the passive MDU is 15-34% of that of the general MDU by year, which shows a sharp decrease compared with the general MDU.
Division | Unit | General MDU to which the Standard for Energy-saving Design by year was applied | Passive MDU | |||
---|---|---|---|---|---|---|
2001 | 2008 | 2011 | 2013 | |||
Annual heating cost | KRW 1000/household | 1,515 | 1,269 | 903 | 691 | 234 |
The results of calculating the construction costs of element technologies related to the general MDU by year and the passive MDU are as shown in Table 13. As for the construction cost of the general MDU, costs for constructing windows, the outside insulation, the ventilation system and a gas boiler, which satisfied insulation performance criteria by year, were added up on the basis of price data (Korea Price Research Center, 2014). As for the construction cost of the passive MDU, additional costs related to the thermal bridge breaker system and air-tightness construction as well as the costs of windows, the outside insulation, the ventilation system and the pellet boiler were summed up based on the estimate of the zero carbon green home validation house. It can be seen that construction costs for the relevant element technologies of the passive MDU increase greatly to the 170-230% level of the general MDU by year.
Note 1: In calculating the construction cost of external insulation system for the passive MDU, cost for installing steel pipe scaffolding is also included unlike the internal insulation system construction.Note 2: When calculating the ventilation construction cost, the duct construction cost, which is applied in common, is excluded.
As shown in Table 14, as for the share of window construction among the construction costs of element technologies related to passive construction, it was found that while it accounted for 30% in the case of the 2001 and 2008 general MDU models, it accounted for more than 40% in the case of the 2011 and 2013 general MDU models and the passive MDU model. As for the share of wall insulation construction, however, it was found that while it accounted for 45% and above in the case of the 2001 and 2008 general MDU models, it accounted for 40% and below in the case of the 2011 and 2013 general MDU models and the passive MDU model.
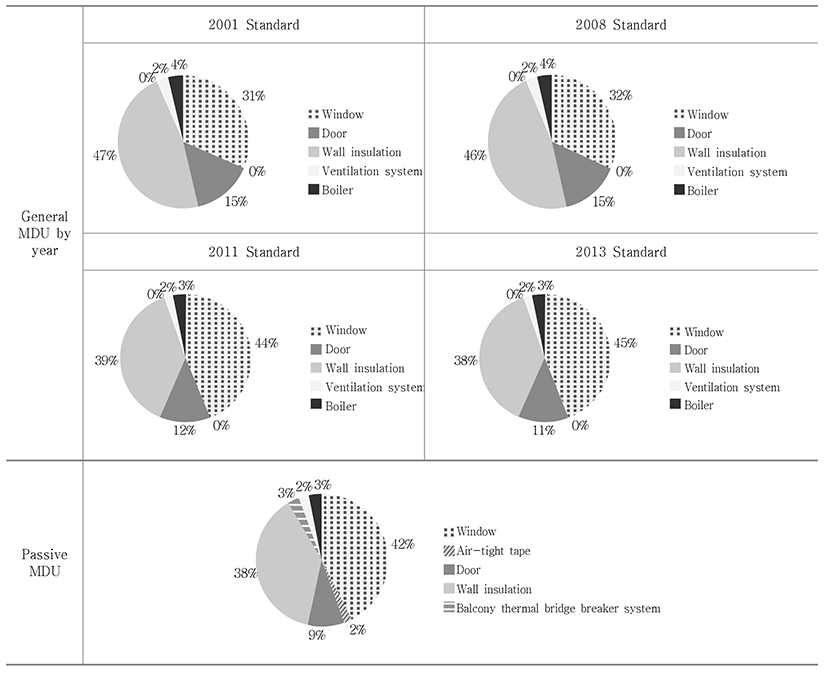
As was the case in the heating cost, it was found that among the general MDU models by year, the 2001 model and the 2008 model showed similar distribution to each other, while the 2011 and 2013 general MDU models showed construction cost distribution similar to that of the passive MDU. In addition, in most cases, among the construction costs of element technologies related to passive construction, the costs of window construction and wall construction account for more than 80% of the whole cost; and thus it can be inferred that for securing the economic feasibility of passive MDU, it is essential to enhance price competitiveness by developing high-efficiency and high air- tightness low-cost windows and outside insulation system.
The factors that influence the economic evaluation of the passive MDU are the saved amount of heating cost and the increased amount of construction cost for the passive MDU in comparison with the general MDU. Here, the construction cost ranges from design cost to successful bid price, and was evaluated in consideration of the bid price rate that influences it. Thus, for the analysis of economic feasibility, the construction cost was calculated with design cost, given the general qualification rate of 87.745 % and the bottom bid price rate of 70%.
First, the results of analyzing the economic feasibility of the passive MDU on a design cost basis, according to the general MDU models by year and the bid price rate are as shown in Table 15. It was found that the payback period varies according to the general MDU models and the bid price rate, ranging from minimum 13.9 years to maximum 41.3 years. In Chapter 3 above, it was judged that the 2001 and 2008 Standards for Energy-saving Design are proper as the standards for the insulation performance of the general MDU model, which acts as the criterion. And as a result of calculating the payback period on the basis of the relevant models, it is found that in case of applying the general qualification rate, the payback period is 17.4 years and 21.3 years, respectively, and that in case of applying the bottom bid price rate, the payback period is 13.9 years and 17.0 years, respectively.
These results of analysis are attributed to the fact that the building construction market at the level of passive MDU has not yet been formed. And it is deemed that at a time when the passive MDU is disseminated popularly, the payback period will become shorter than the present level, for the price competitiveness of related element technologies will be achieved then.
In 2009, the government announced a road map for greenhouse gas emission reduction that requires all new houses to comply with the standards of passive house from 2017. Assuming that the passive MDU would be applied in 2017, this study analyzed the trends of the annual heating energy cost and the construction cost for the general MDU by year and the passive MDU.
As shown in Fig. 7, as for the annual heating cost, it is shown that the heating cost decreases gradually from the general MDUs to the passive MDU owing to enhanced insulation standards. As for the construction cost of relevant element technologies, however, it is shown that in the case of the general MDU models, it increases at similar levels according as insulation standards by year are enhanced, while in the case of the passive MDU, it rises steeply. The analysis shows that such a rise in the construction cost of the passive MDU is attributed to the fact that high air-tightness & high insulation windows and doors, the outside insulation system, and the pallet boiler are priced high because they are not yet supplied amply in the market.
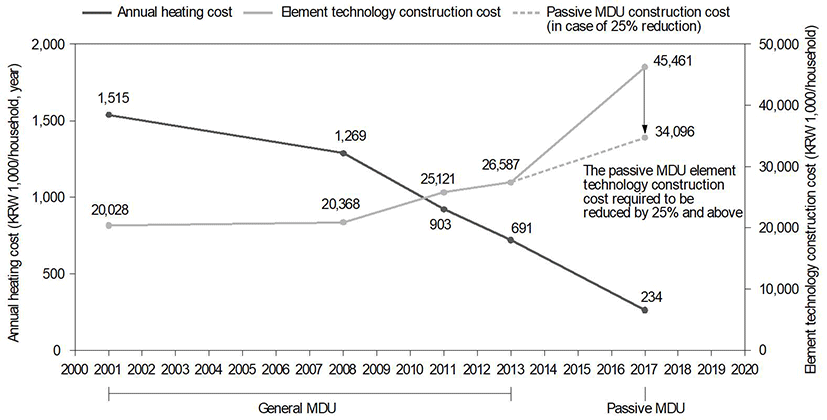
Thus, for the vitalization of passive house dissemination, it is necessary to create the building construction market of improved price competitiveness for performance, with respective to high-performance windows and the outside insulation system. For this, it is necessary to disseminate low-cost products by investing in technology development related to windows, the outside insulation system, and air tightness. On the other hand, to achieve the target for passive house performance and vitalize the dissemination of passive houses by 2017 according to the road map of the government, it is necessary to review the road map and prepare direct and indirect support methods through detailed stepwise investigation so that the passive MDU may be established successfully, rather than strengthening the standards of insulation performance abruptly.
V. Conclusion
This study intended to prepare data for reliable economic evaluation, aiming at invigorating the dissemination of the passive MDU. The results of analyzing and comparing the general MDU models, to which the Standards for Energy-saving Design by year since 2001 were applied, and the green home model, which is the passive MDU, with respect to heating energy consumption and economic feasibility, are as follows:
First, as a result of calculating the annual heating energy demand for the general MDU by year and the passive MDU, it was found that the annual heating energy demand of the passive MDU was 17-36% of the general MDU, showing a great decrease in the heating energy demand.
Second, as for the general MDU, heat loss from windows was 38-54%, accounting for the greatest portion among its heating energy demand. And as progress was made towards the passive MD, insulation was reinforced, and ventilation heat loss increased relatively. Therefore, it is estimated that in the future, it will be necessary to prepare alternatives that can reduce heat loss from the ventilation part of the passive MDU.
Third, it is estimated that the general MDU models to which the Standards for Energy-saving Design in 2001 and 2008 were applied reflect well the characteristics of general MDUs, and are suitable as the model of general MDU, which acts as the criterion for economic evaluation,
Fourth, among construction cost related to passive construction, the cost of window and wall insulation construction accounted for more than 80% of the total cost. And thus it is necessary to enhance their price competitiveness in order to secure the economic feasibility of passive MDU, by developing low-cost high-efficiency and high air-tightness windows and outside insulation system.
Fifth, as a result of analyzing the economic feasibility of passive MDU in comparison with general MDU models, it was found that in case of applying the general qualification rate, the payback period is 17.4 years and 21.3 years, respectively, and that in case of applying the bottom bid price rate, the payback period is 13.9 years and 17.0 years, respectively.
The reason for the current high level of passive MDU construction cost is that high air-tightness & high insulation windows and the outside insulation system, which account for the greatest parts of passive MDU construction cost, are still at a developmental stage, and maintain high prices. If the market of price-competitive high air-tightness & high insulation windows and outside insulation system is formed in the future, it is forecast that passive MDUs with a payback period of around 10 years will be disseminated. This study carried out investigation on methods for economic evaluation, focusing on the heating energy part of the passive MDU for unit household. In the future, it is necessary to perform the economic evaluation of passive construction work-related parts in terms of the concept of MDU complex. In addition, the total energy consumed by a residential building includes cooling and electric energy as well as heating energy; therefore, new and renewable energy electricity supply system such as photovoltaic system should ultimately be included in the economic evaluation. As a follow-up study in connection with this, it is necessary to carry out a study on methods for the economic evaluation of passive MDU complex, including cases in which the renewable energy system such as photovoltaics is installed.